Where are Hungarian car parts manufacturers heading?
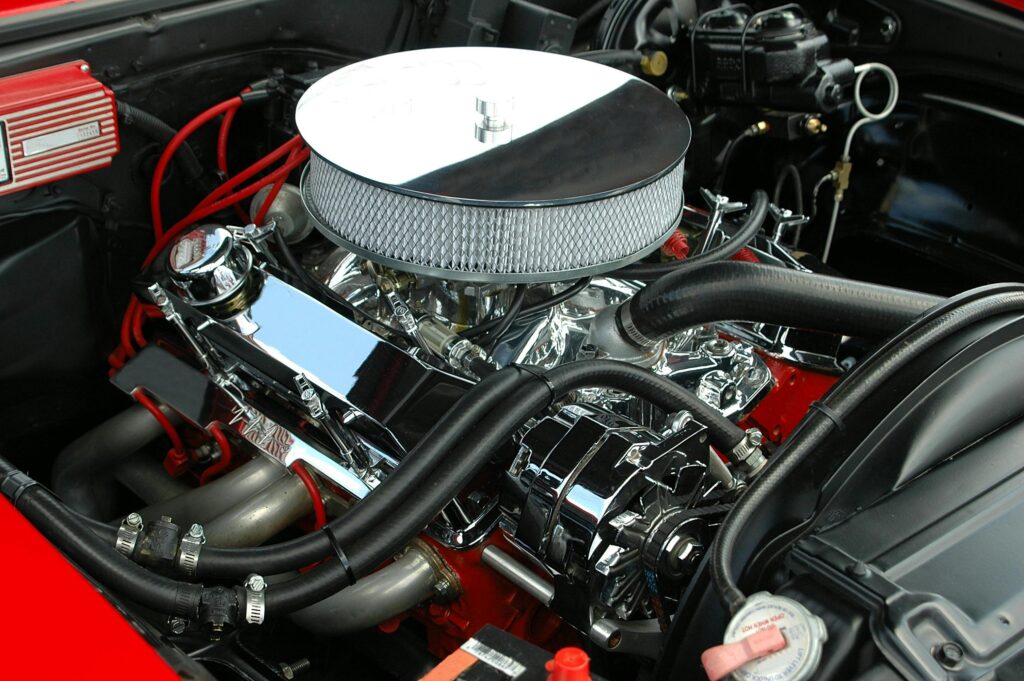
The Hungarian automotive industry has faced a shortage of demand in recent years, following the coronavirus pandemic, the chip shortage, production difficulties, and the energy crisis. This lack of demand has become increasingly intense since the summer of 2023. The automotive industry and the manufacturing of electrical equipment (including battery production) have shown a greater decline than the average for the manufacturing sector. This deteriorating performance is also affecting the labor market. Although large-scale layoffs have not been typical, the slowdown in the global and German automotive industries led to a significant decrease in the number of employees in Hungary in 2024, according to data from the Hungarian Central Statistical Office (KSH). Several major suppliers also experienced substantial reductions in their workforce. The most significant decrease in employee numbers was observed in smaller and medium-sized Hungarian-owned companies. The situation of companies is also influenced by their position within the industry’s value chain.
The business results for 2024 are not yet known, but there was no drastic change in profitability between 2019 and 2023. Significant changes are expected this year due to the decrease in demand and the transition to electric vehicles. The capacity utilization of European car manufacturing has significantly decreased, particularly in Germany and Italy. The shift to electric vehicles requires less capacity, and demand in this segment is also lower than expected. Europe is simultaneously experiencing a decline in electric car sales and a general decrease in demand. The prospects of companies are determined by the products they manufacture and the development of their order books. Suppliers lower down in the value chain may face challenges due to the decrease in demand or if their customers start manufacturing electric vehicles and they cannot adapt to this change.
The most significant change has affected tier 1 companies, which are direct suppliers to OEMs (Original Equipment Manufacturers). These companies were more profitable than OEMs in the years before Covid, but this has since reversed. OEMs require less labor but are committed to avoiding large-scale layoffs, so they are increasingly manufacturing components, such as electric motors or inverters, themselves, which they previously purchased from suppliers. This further reduces demand for suppliers. Large companies are forced to cut costs, which can lead to factory closures or reorganizations. Hungarian subsidiaries are theoretically in a more favorable position due to lower local costs, but the rate of workforce reduction was not significantly lower than in Germany. The interest of OEMs and tier 1 suppliers is to maintain the functioning of the supply chain, but this is not a conflict-free process in the current situation. Significant cost pressure is being placed on suppliers. Some companies are less affected by the crisis because approximately one-third of their products go into traditional models, one-third into alternative powertrain models, and one-third are powertrain-independent. Companies are also facing greater pressure during cost-sharing negotiations. Customers may favor more stable suppliers to ensure security of supply.
However, the downturn also presents opportunities for suppliers. Due to the problems of many smaller Western European suppliers, tier 1 customers may look for new partners among Hungarian suppliers. Companies that can diversify and supply to multiple programs will not experience a decrease in their order books. If European car production recovers, these Hungarian suppliers can expect significant revenue growth. However, those who cannot adapt will struggle to survive the market’s normalization.